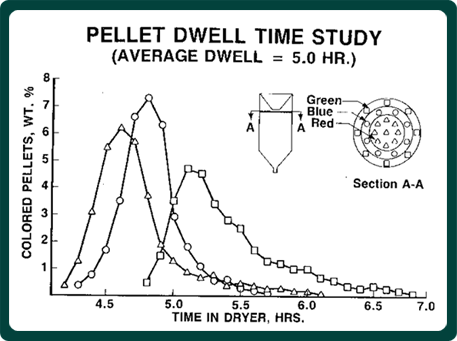
Even though all dryer hoppers have cones in the center, the resin in the center still moves quicker through than the resin that lands close to the hopper wall. So you will have to make a compromise for your temperature/time setting. If your plant has the lab to do so, check the AA content with various settings.
Material can be over-dried and under-dried. The latter is more common than the former and can have a variety of reasons. It is often not easy to determine the dryer as the source of the problem. That is because hazy preforms for example could be the result of a non- performing dryer or poor processing in the injection machine. Most of the time, the processing personnel will try their bag of tricks and eventually call maintenance to check out the dryer.
A minimum dewpoint of -40 F
Dewpoint switch-over instead of time based switch-over of desiccant beds. It is more economical to switch over only when the dewpoint goes above -40 F and it extends the life of the desiccant.
A visible and audible alarm on the dryer with clear error messages that everyone can understand.
A thorough training program for personnel of all shifts to interpret these error messages and take proper action.
Consider gas-fired dryers. They are more economical.
Several companies now offer features that detect the dryness of the PET. I have no experience with these dryers and dread the added complications. If anyone can give me some feedback, I would appreciate an email.